在细胞与基因治疗领域,质粒DNA作为病毒载体(如AAV、慢病毒)或mRNA疫苗生产的核心原料,其生产工艺的效率和稳定性至关重要。碱裂解是质粒生产中的关键步骤,直接影响质粒的收率、纯度和可放大性。本文将基于科百特质粒全工艺链解决方案(如图1),针对质粒的关键生产环节,如在线连续流碱裂解系统E-lystem®、专用澄清滤器Claricap® CSD、阴离子膜层析Pultrix™ XQ等产品应用的技术整合,将质粒工艺最简化,尤其适用于细胞与基因治疗或动物疫苗领域对高纯度、大规模、低成本质粒的需求,实现其高质量的工艺稳健性、合规性和商业回报上的综合价值。以下将重点突出科百特如何通过创新技术实现质粒DNA的高质量、高效率生产,同时降低工艺复杂度与成本。
1. E-lystem® 在线碱裂解系统
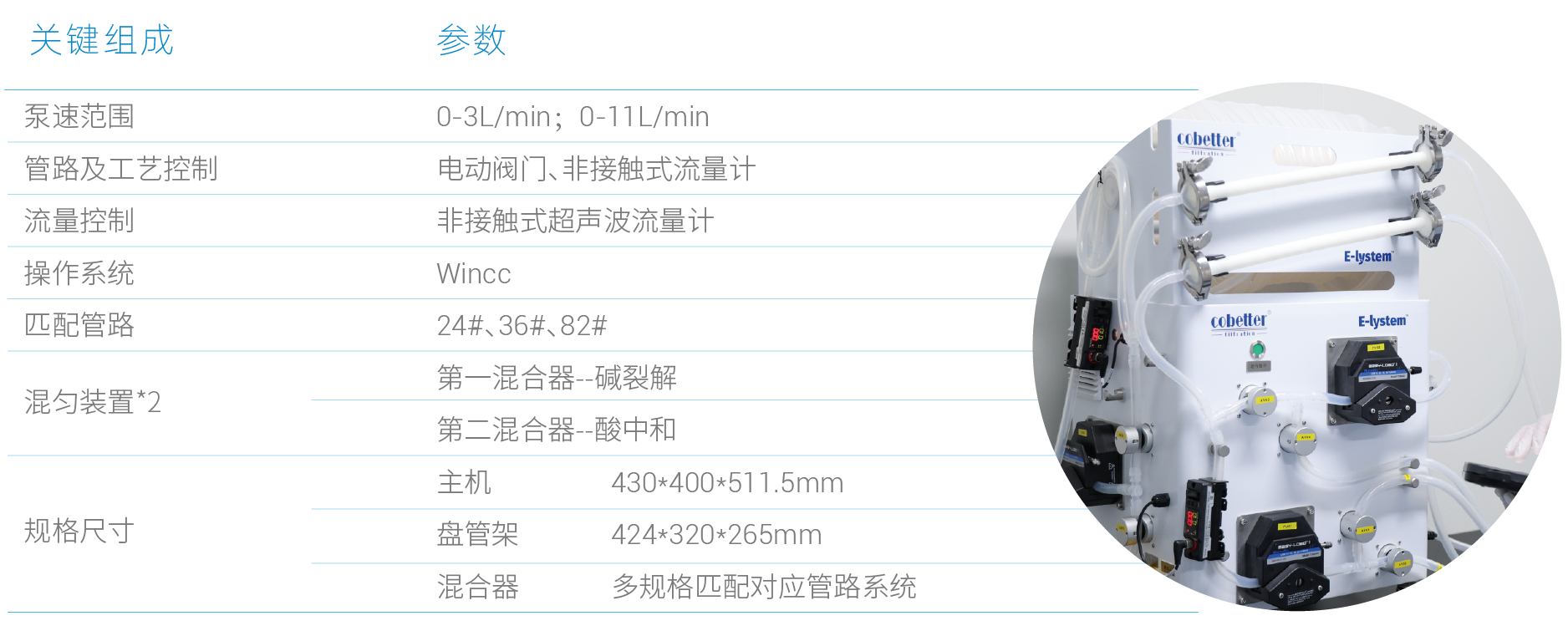
碱裂解工艺的痛点与挑战
当上游发酵工艺确定后,其碱裂解步骤是质粒生产的“卡脖子”环节,传统批次工艺的局限性包括:
· 反应条件难以精准控制;
· 局部过碱:批次混合不均可能导致局部pH>12.5,引发质粒不可逆变性(超螺旋结构损失);
· 剪切力损伤:机械搅拌易破坏超螺旋质粒分子结构,尤其 大分子质粒(>10 kbp);
· 放大效应显著,批次工艺在放大时混合效率下降,收率与 质量(超螺旋比例)波动大,批间一致性难以保证;
在线碱裂解系统的技术优势
该系统通过模块化“微流控”设计,实现裂解所需物料间的高效、温和且均一的精准混合控制,以解决传统工艺的痛点:
(1)工艺原理与流程
· 模块化连续流反应器:菌体悬液与裂解液(NaOH/SDS)通过高精度泵按比例输送至特定结构的混匀装置,实现快速混匀并确保物料温和受力,充分裂解以实现产量最大化,同时,可避免传统批次工艺的局部过碱(pH>12.5)风险,以及过度搅拌带来的过高剪切应力造成质粒超螺旋结构的破坏。
· 精确裂解时间:通过可调流速与反应管道长度精确控制裂解时间(2-5分钟),避免过度裂解,最大限度保留超螺旋质粒结构。
· 在线中和:裂解后高粘度裂解液与酸中和液连续高效混合,快速将pH降至中性(pH 5.0-5.5),高质高量的实现质粒复性并沉淀宿主DNA/蛋白及SDS复合物。
(2)关键优势
· 提升质量与收率:
· 超螺旋质粒比例稳定在95%以上(传统工艺60-80%),减少线性/开环质粒杂质。
· 质粒收率提升,无机械搅拌,剪切破坏低,质粒完整性保留率提升。
· 放大友好性&体量灵活
· 线性放大,无混合效率损失,适合商业化规模(100L/h左右)。
· 降低成本
· 试剂消耗低:精准投料,无批次浪费,无系统滞留损失。
· 生产时间缩短50%(连续处理 vs 批次间歇操作)。
· 符合GMP要求
· 一次性管路系统及混合装置,可避免清洁验证
· 封闭系统减少污染风险
2. Claricap® CSD质粒专用澄清滤器:单级高效截留去除沉淀及杂质
技术原理
· 深层过滤+弱电荷修饰:采用多层复合滤材(如纤维素/硅藻土+电荷修饰表面),通过尺寸排阻+静电吸附双重机制捕获细胞碎片、SDS-蛋白复合物及宿主DNA,并几乎无目标产品损失。
· 专为质粒澄清设计:优化滤器结构及膜精度选型,单级应用即可兼顾高载量及高控浊效果,滤后浊度<5NTU。
工艺简化与优势
· 一步替代多步澄清:传统工艺需离心+深层过滤或多级PP囊式/除菌滤器,该专用滤器亦可直接在线连接连续流系统,实现裂解-中和-澄清一体化。
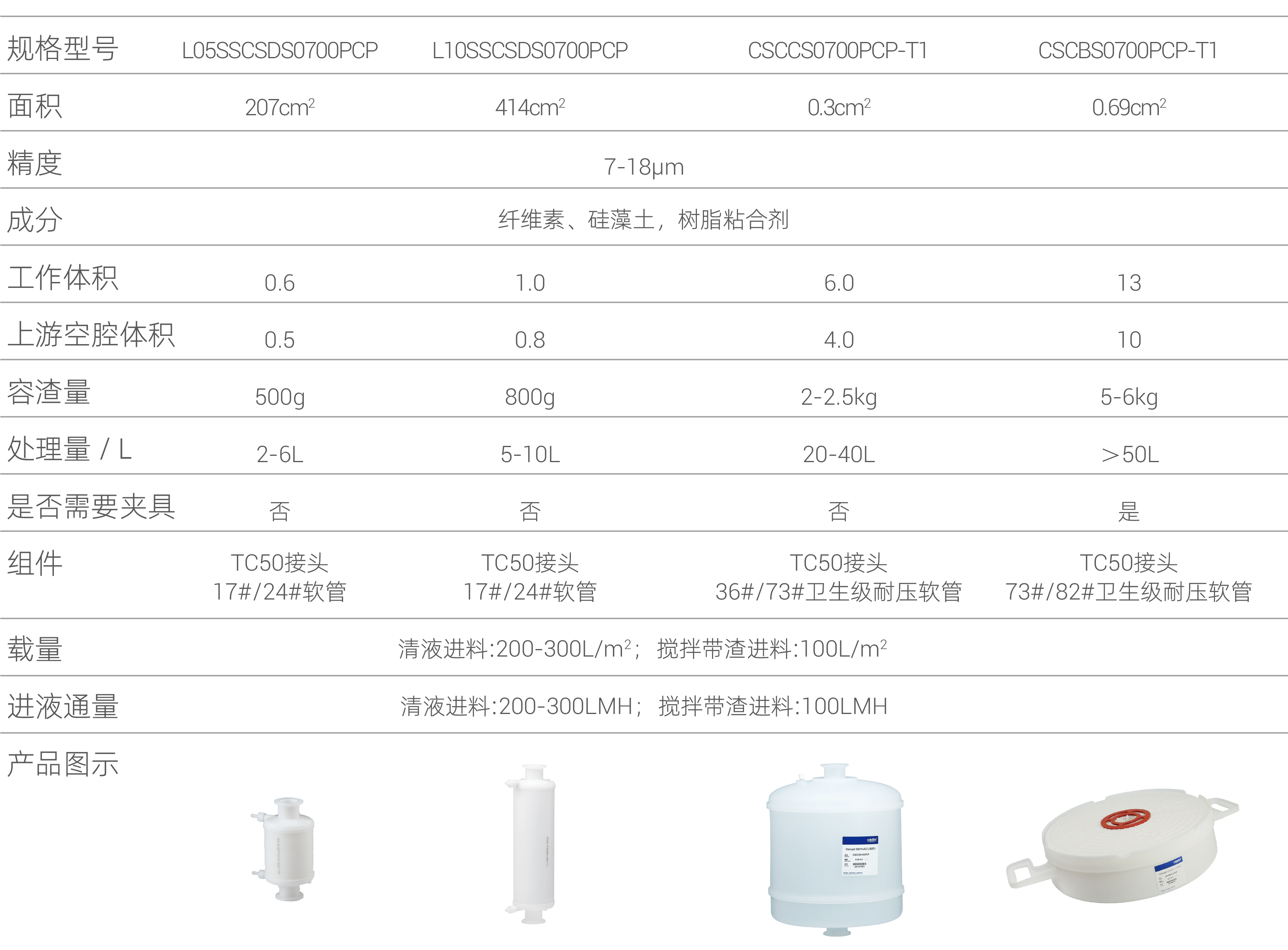
3. Pultrix™ XQ阴离子膜层析:高载量快速纯化
技术原理
膜层析 vs 传统树脂层析:
· 阴离子交换膜(如磺酸基修饰):利用质粒DNA在相对高盐下与膜表面正电荷结合与膜表面正电荷结合,高盐洗脱。
· 对流传质模式:质粒直接接触膜表面结合位点,传质效率传统填料高10-100倍,载量提升至5-10 mg/mL(传统填 料柱仅1-2 mg/mL)。
工艺简化与优势
· 快速纯化与集成化:结合在线裂解-澄清系统,直接上样澄清液,省去预浓缩和分子筛步骤;质粒纯化捕获时间缩短至0.5-1小时(传统预浓缩加分子筛需4-6小时)。
· 高分辨率与收率:一步去除宿主RNA、内毒素、蛋白质,质粒纯度>95%(HPLC检测); 收率>80%(树脂柱收率60-70%)。
· 规模化灵活性:膜层析模块可堆叠放大,支持单批次处理百升级裂解液。
综上,通过以上关键环节:在线连续流碱裂解系统、专用澄清滤器和阴离子膜层析的应用整合,将质粒工艺生产实现了:
· 质量精进:超螺旋比例>95%,纯度>98%,工艺稳定性(CV<5%);
· 工艺最简化:工艺时间缩短50-70%,耗材成本降低20-60%;
· 规模化无忧:从研发到商业化无缝放大,符合GMP与连续制造趋势。
科百特聚焦质粒生产核心痛点,如质量波动、成本高、工艺复杂,将质粒工艺路线简化、质量精进,实现降本增效同时,其各环节也具备突出的产能灵活性与合规性,助力企业从“传统批次”向“集成连续化”生产模式升级。